Inspection Operations, especially Receiving Inspection, are not included in Process Flow Diagram.
Input in Column : Product Characteristics (may be defined as Desired Outcomes or Outgoing Dimensions) are not covered Product Characteristics relating to supporting activities such as clamping or locating,… in next operations. Use of Characteristic Matrix will help to define all related characteristics.
Number of Operation Symbol defined in Process Flow does not reflect all sources of variation such as Number of Sub-contractors, all location of stores (outside and inside), number of machines.
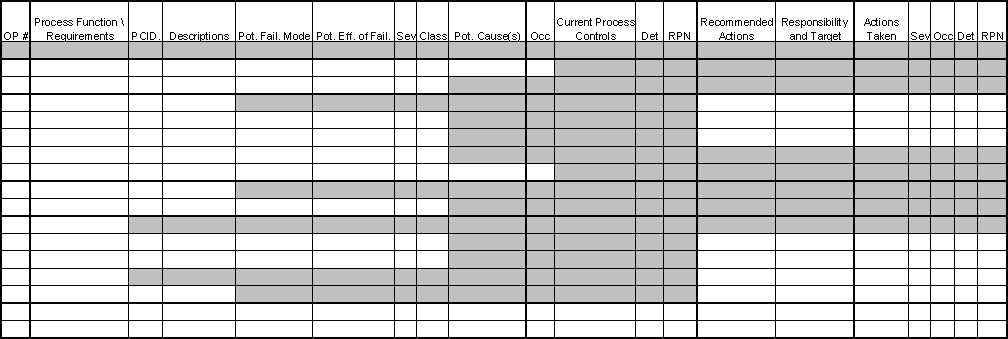
Typical error and TIPs for Process Failure Mode and Effect Analysis
- Failure Modes from previous operations are included in analysis in considered operation, that leads to repeated reference of Failure Modes between operations. And the Potential Causes of repeated Failure Modes will not be defined as clearly as done by the directly-related operation’s analyzer. (Note : The directly-related operation is the operation responsible for creating Product Characteristics of which Failure Mode considered.)
- Defining of Failure Mode in some particular operation, some may put “Fail inspection” or “out of Specification” as failure mode inspection operation which is actually should be the failure mode of previous operation(s) producing that bad product characteristic (Failure Mode).
- There is confusion between “Potential Failure Mode” and “Potential Causes”. This incidents are frequently happen in real situation when you team up all APQP/Process Review Members and the very first input you will have during brainstorming is all the sufferings from customer (:- next process Customer, OEM customer, end user of product, all issuer of regulation (Government or States) suddenly you will add in “Potential Effects of Failure Modes” Column. Here, the confusion arises, because there is tendency to put the failure modes into “Potential Causes” Column and some may put the effect or additional description of specified Effects into Potential Failure Mode” Column in stead.
- Most of Failure Mode Analysis can be operation-oriented failure mode analysis. But for complex or automated operations which be able to create many PCID at a time, not all PCIDs are considered for their failure modes. Therefore, to comprehensively define all of the failure modes under one particular operation, you should add PCID (or Product Characteristics, Desired Outcomes or Outgoing Dimensions) column and description before considering Potential Failure Modes.
- According to PFMEA form, there are some information (in columns) which can be expanded or branched as appropriate during further analysis, namely from left to right, Operation Number/Description, Product Characteristics (PCID), Potential Failure Modes, Potential Causes and Current Control.