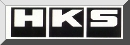
Detailed Instructions to Install FCD and Increase Boost
REVISION HISTORY:
July 16, 1995 - Initial version
July 24, 1995 - Added Warning about STP octane booster.
WARNING: What you do to your car is what you do to your car.
WARNING: After finishing installation of these devices you will have
effectively eliminated your stock protection against
waste gate failure (unless there is some other stock system
that I am not aware of.)
WARNING: increasing turbo boost above 17.5 psi is not recommended and
could cause severe damage to either your turbo or engine or
both, unless you have made significant modifications to your
engine such that it could withstand such high boost pressures
and that you have also installed some aftermarket superstock
turbo charger.
WARNING: There seems to be a very narrow range of restrictor hole size
to turbo boost pressure correlation. So if you decide to get
the Nth pound of boost from your turbo, then be very careful
in proceeding. Remember there appears to be just over
.011 thousandths of an inch between just 2 pounds of additional
boost and boost that will destroy, a word to the wise.
WARNING: the specific results that you obtain doing this proceedure will
depend on where you are in relation to sea level. My tests were
done at or very near sea level. I would suspect that if you
lived in Wyoming or Colorado that the specific boost that you
would get would be less than if you were at sea level.
There are also many other factors that will change the specific
boost that you get, all too many to mention in this article.
NOTE: this proceedure asks you to disconnect the NEGATIVE battery terminal
so if you have your security set on your radio, you will need to
go through the erase proceedure outlined in the owners manual
BEFORE you disconnect the negative battery terminal.
NOTE: these proceedures make the following assumptions:
1. That you have already installed the HKS Super PowerFlow
air filter (for specific questions call HKS)
2. That you have installed the Jacobs OmniPak ignition system with
Jacobs EnergyCore wires, and a Jacobs Solid Core OmniPak to
distributor center wire.
3. That you have installed AC Delco RapidFire Spark Plugs properly
gaped to .035 and properly indexed them.
4. That your stock boost level is specifically 10 psi to start with.
5. That you have a set of MR2 shop manuals (almost a must).
6. I used one bottle of STP octane booster before filling up (See below!)
WARNING: from my experience, I would suggest NOT using
STP octane booster it could foul your plugs
and give your car generally poor performance.
In its place I might suggest using 104 octane booster.
NOTE: Please consider all measurements, test results, readings and other
such data as APPROXAMATIONS, as each specific MR2 may or may not be
set up the same as mine, then your specific findings may or may not
be exactly the same, there are just too many varables in the
equation.
TOOLS USED:
25 watt soldering iron
NOTE: HKS provides mechanical taps and bullet connectors which I
found would either make a questionable connection or would be
very difficult to work with and install given the very limited
space and wire length you will have to work with.
This is part of the reason that I chose to solder all of my
connections, thus I know for sure that they will not come loose
and will be a good solid connection.
60/40 resin core solder
sharp knife
small #1 philips screw driver
drop light
10mm open end/box end wrench (wrapped with electrical tape)
roll of black electrical tape
10 inch #2 philips screw driver
pair of pliers
pair of long needle nosed pliers
small electric drill
small drill bit, specifically .0775 thousandths inch (4 psi boost)
small drill bit, specifically .0885 thousandths inch (2 psi boost)
10 lb bar bell plate or some similar weight object.
PARTS PURCHASED:
HKS Fuel Cut Defencer
6.5 inches of 1/4 fuel line NOTE: 1/4 is ID of line not OD
low pressure welding gauge 0-30 psi range, with a standard
1/8 NPT male fitting.
Adapter to adapt male NPT fitting from gauge to 7/32 vacuum line.
10 to 12 feet of 7/32 (15.6mm) standard vacuum line.
small plastic tee that can adapt to 1/8 vacuum line and 7/32 line.
I used a small tee that had graduated increments on it such that
as you proceed up the length of one of the legs of the tee that it
gets progressively larger.
small 2 inch piece of 1/8 vacuum line
Nylon Printed Circuit Board stand off, can be purchased at most good
electronics stores.
NOTE: specific size and design is critical to operation.
Specifically the Nylon standoff is:
.317 in diameter
1.250 long
center threaded holes (PART WAY THROUGH), threaded hole diameter
.107 inch, (NOTE: I do not know how important the size of the
threaded hole is to this operation. It may make no
difference at all.
Substitutes could be used if you can not find a nylon PCB standoff.
I suspect that a piece of metal such as aluminum or brass or the like
would do just as well, as long as it as very near the same specific
dimensions.
OPTIONAL PARTS:
Two one inch pieces of 1/8 shrink tube
Two small 1/4 fuel line hose clamps
various sized drill bits in .001 or .002 thousandths increments
from .0885 down to as small as .0700
NOTE: I used a .061 thousandths hole in one of the restrictors
and it caused the boost to be able to go VERY MUCH
HIGHER than 15 psi. So I would warn against using a
restrictor size hole that small.
FIRST PROCEEDURE TO INSTALL THE HKS FCD (fuel cut defencer)
Assemble all tools and parts needed, plug in your soldering iron and let
it get hot. Open the front lid, and proceed to remove the spare tire.
You should now see the battery. Using your 10mm openend/boxend wrench
loosen the RIGHT terminal (US cars), ie.(the terminal that does not have
a red rubber cover over it.) After loosening the nut, then wiggle the
terminal off the battery post, and move it over to the side making sure
that it doesn't flop back and make connection or touch the negative post
of the battery.
Now proceed to open the rear trunk lid, and setup your drop light so that
you can clearly see inside, start over on the left side ie.(drivers side)
and note diagonally down from the small trunk light about 8 inches or so
there is a black plastic push rivet, look up now towards the upper edge
and as you look across the rest of the trunk you will notice 4 more
black push rivets, to remove them, use the small #1 philips or some
small punch, and push gently on the center of the rivet, do not push it
so hard that you push the center piece all the way through, push it only
just an 1/8 inch or so, and you should feel it click slightly. Proceed
across the trunk liner pushing the center pin and then pulling out each
of the five push rivets. Set them aside for now. Now pull down the trunk
lining, along with the hard board backing piece that covers the PCME.
Now using your 10 lb barbell plate, or some similar weight, put it down
on the trunk lining to hold it out of your way while you work.
The PCME is the large metal box in front of you now. There are three
connectors across the bottom of the PCME. We will be installing the TAP
wires first, and then the PIM wire last.
Now we are going to mount the HKS FCD on the face of the PCME box using
the HKS kit supplied double sided adhesive patch. Peel off one side of
the cover on the adhesive patch and stick it in the center of the
FCD, then peel off the other cover of the patch and press the FCD just
about near top center on the PCME box. You can pre-measure the wire
lengths, but as mine mounted I did not have to cut any length of wire
from any of the wires on the FCD.
NOTE: before proceeding to pull out these connectors, please make sure
that you touch a good ground point, and make sure that you have
built up no static charge before touching these connectors.
NOTE: unless you have a photographic mind, then deal with only ONE
connector at a time. Never pull out all three connectors unless
you have your shop manuals.
The locking tab for each of the connectors is front center, observe the
left connector, and push the lock tab in and at the same time pull down
(wiggling), the plug, and it should come out of its female receiver.
Now NOTE: connector orientation is critical to this operation, there are
two different views, one that the HKS instructions show, and one that the
shop manuals show. I had to use both to make sure that I had the
connector oriented properly. The HKS diagram shows the plug as though
the lock tab were on top, with the wires pointing out at you. Of course
this is completely different than the way the plug naturally comes out of
the PCME. As the plug comes out of the PCME, and you just push the plug
downwards, the lock tab is on the bottom of the connector, and the wires
are going away from you. So in order to get HKS's view, you would have to
pull the connector, and then loop bend it back so that the lock tab is
on top and the wires are pointing at you.
Now the shop manual diagram is completely different than that, in the
shop manual the connectors are shown with the lock tab on top but with
the wires going back away from you, and the front of the connector
pointing towards you.
So it is important that you have it clear in your mind the proper
orientation of the connector so that you get the proper wire.
As it would probably use up volumes of explaination, I will leave this
up to you and hope that the above info is sufficient for you to
make sure that you have the proper wires selected. In my case I had to
correlate between the two diagrams inorder to make sure that I had the
proper wire.
NOTE: on each of the connectors I had to remove black tape that is used
to bundle the wire group together inorder to have sufficient space to
work with the wire. Remove this stock black tape as necessary to get at
the wire bundles. I did not think it necessary to replace the tape after
finishing this proceedure.
Nuff said about that, now on with the show. As you have now pulled out
the left connector from the PCME, orient the connector such that you can
find the E1 ground wire. The E1 ground wire is brown and we will be
connecting the black wire from the FCD to it. After you have properly
isolated the brown E1 wire on the connector then using a knife, carefully
shave off about 1/8 to 1/4 inch of insulation down about 3/4 inch from
where it comes out of the connector body. DO NOT CUT THE E1 WIRE.
This is a TAP joint.
After having removed the portion of insulation on the brown E1 wire then
wrap the already stripped end of the black wire from the FCD to the
brown E1 wire. Make a fairly good mechanical connection, and then using
your solder iron and a little solder, solder the connection.
Now take a small strip of black electrical tape, 1/4 inch wide, and about
an inch and a half long, and wrap the connection. When you are satisfied
with the connection, then position the plug and press it back into place
in the female connector on the PCME, make sure that the lock tab clicks
in place.
Now we are ready to do the second tap connection on the right connector.
Focus on the right most connector on the PCME and press the lock tab down
and pull and wiggle the connector out. Once this is done than using the
HKS diagram and your shop manual get the connector properly oriented so
that you can find the +B battery wire. The +B wire is a Black/yellow
striped wire. Orient the connector and find the wire. After you have
isolated the wire, then doing basically as before, eye-ball a distance
just down from the connector body about 1/2 to 3/4 inch and shave off
about 1/8 to 1/4 inch of insulation from the wire. DO NOT CUT THE WIRE.
After you have done this then find the red wire comming off the HKS FCD
and make a good mechanical wrap onto the black/yellow striped +B wire.
Now using your soldering iron and solder, solder the connection.
Orient the wires now so that you can wrap your electrical tape on them
and using a 1/4 wide piece of electrical tape about an inch and a half
long, and wrap the connection. When you are satisfied with the
connection then position the connector on the female connector on the
PCME and press it back into place making sure that the lock tab click in
place.
Now we are ready to do the last connection, the PIM wire on the center
PCME connector. So now press the center connector lock tab and pull and
wiggle the connector down out of the female connector on the PCME and
orient it so that you can find the Light-Blue PIM wire. It is the only
Light-Blue wire on the connector so it is really not hard to find.
You will have to remove the black electrical tape that came stock on the
wire bundle to give youself sufficient room to work with the wire.
Isolate the wire and half way between where it comes out of the connector
and where it disappears back into the wire bundle then cut the wire at
that halfway point. This cut should leave you sufficient room to now
strip about a 1/8 to 1/4 inch length of insulation from each end of this
Light-Blue PIM wire.
NOTE: at this point if you opt to you can use a small piece of 1/8 inch
shrink tube to seal these connections if you wish otherwise you
can wrap them with electrical tape as you did the others.
If you do use shrink tube make sure that you put the piece on
over the wire before you solder them together.
Once that is done then find the yellow wire comming from the HKS FCD and
make a good mechanical wrap together of the wire comming directly from
the PCME connector. Wrap this yellow and half of the Light-Blue wires
together and then using your solder iron and a little solder, solder these
two wires together.
Now either heat your shrink tube or wrap the connection with a small 1/4
inch wide about 1.5 inch long piece of electrical tape.
We are ready to connect the other half of the PIM wire to the White wire
comming out of the FCD. So wrap these two wires together, the white FCD
wire, and the other half of the Light-Blue PIM wire as it comes out of the
wire bundle. Of course either first sliping over the wire your shrink
tube, or wait and wrap the connection with tape.
After you have secured both connections of the PIM wire and you are
satisfied with the connections then position the connector and press it
back up into place in the female connector on the PCME. Making sure that
the lock tab clicks in place.
Now check your work, and make sure that you are satisfied with the wiring.
Now do a little clean up work, and you are ready to put the trunk liner
back in place. Press the trunk liner back up in place and then find one
of the push rivets and slide the center pin up so that the blunt end of
the center pin extends about 1/8 inch or so up above the flat top piece.
Then carefully press the rivet back into the hole starting in the left
corner and working your way across the trunk. Press the center pin so
that it is flat with the top of the rivet top and it is in place.
Check the right side of the trunk liner where it is cut for the trunk
hinge, I had just a little trouble putting this area back in place.
Now after cleaning up the rear trunk area, we are ready to put the
Negative terminal back on the battery, so position the negative terminal
on the battery post and using the 10mm openend/boxend wrench tighten down
the nut on the terminal. Make sure it is nice and tight.
Now replace your spare tire, and at the same time you might check the
air pressure on the tire and make sure it is up to the correct pressure.
Now you can start the car and observe that the engine runs normally.
=======================================================================
Proceedures to increase stock turbo charger boost.
NOTE: again this proceedure assumes that your stock boost pressure is
at 10 psi, of course if it is different you will obtain different
results.
We will first manufacture our restrictor. locate your 6.5 inch piece
of 1/4 fuel line, your nylon stand off, and your drill bit of choice
either the .0885 for two pounds of boost above stock, or the .0775 drill
bit for four pounds of boost above stock.
Locate your nylon PCB standoff, and making sure that the center threaded
hole is not all the way through, chuck up your drill bit of choice and
carefully drill out the center of your nylon standoff.
Now locate your 6.5 inch piece of 1/4 inch fuel line, and cut it exactly
in half, now where you cut it press one half of the fuel line on the
nylon stand off, and press the other half of the fuel line on the
remaining half of the nylon standoff so that you now have one continuous
assembly. If you have the proper size diameter nylon standoff then it
should press fit into the inside of the 1/4 fuel line very tightly such
that there is no chance that it will slide off. If you are concerned
then I would suggest using the optional small 1/4 inch fuel line hose
clamps at this time and clamp one down on each side of where the nylon
standoff is located in the center of the hose assembly.
We will be using the stock hose clamps from the stock waste gate actuator
hose to secure the ends of our new restrictor hose assembly.
In order to get at the waste gate actuator hose we will have to move
a few things out of the way first.
Proceed to lay out your tools as you will need them and open the engine
compartment, and as you are on the drivers side (US), lean over and
observe the large hose assembly as it comes off the mouth of the intake
side of the turbo charger. Using a long 10 inch #2 philips screw driver
loosen the hose clamp that tightens down on the mouth of the intake side
of the turbo. NOTE: don't do as I did and drop the screw driver down
behind the turbo charger housing, and take an additional 30 minutes to
retrieve it.
On my engine this end of the large rubber assembly easily came off the
turbo charger mouth. Now, look up and over to where the hard plastic
elbow goes into the short rubber piece that connects to the air flow
meter. Loosen the hose clamp on the elbow side. This elbow was just
a little sticky even from when I pulled it off when installing the
HKS powerflow.
Now you will observe about halfway down this assembly two hoses one large
one small going into the side of the large rubber hose piece. One of
the smaller hoses is from the PCV valve the other is a metal hose/pipe
that comes up and into the air bypass valve. This is personal preference
but disconnect one end or the other of both of these hoses, I chose to
disconnect the air bypass valve up top side because the screw hose clamp
is much easier to get at than the squeeze clamp down on the large rubber
hose assembly. I also chose to disconnect the PCV valve where it comes
out of the large rubber hose assembly, and slide the two inch long pipe
connected to it out of the side.
Once this is done then you can wiggle loose the entire large rubber hose
assembly including the hard plastic elbow, and pull it off the turbo
charger mouth and at the other end pull the hard plastic elbow out of
the end of the air flow meter. Set this assembly aside for now.
Now you have sufficient working space to get at the waste gate actuator
hose. Observe a small fitting with a rubber hose attached comming out
of the upper right side of the turbo charger, it then loops a short loop
over to the small fitting on the LEFT side of the waste gate.
Using a pair of pliers carefully squeeze the hose clamp on the turbo side
fitting, and pull the hose off this turbo fitting. Then making sure
that you have a firm grip on the hose, proceed to squeeze the hose clamp
on the left side of the waste gate, and pull the hose off this fitting.
NOTE: I used a long pair of needle nosed pliers to get at the hose clamp
on the waste gate side, as it is fairly tight quarters.
You should now have a very short sort of U shaped piece of hose.
Remove the two hose clamps one on either end of the hose and set the hose
piece aside. NOTE: I did not modify the stock hose piece incase I want to
at some later date replace it.
Now locate your manufactured restrictor hose and slide one hose clamp on
either side of it. Slide them down about a half inch or so.
Holding your manufactured restrictor hose in your left hand (I'm right
handed), press one end of the hose up onto the left side waste gate
fitting. You will have to use a small pair of long needle nose pliers and
squeeze the hose clamp and at the same time pushing with your left hand
and pulling with your right, slide the hose up onto the fitting as far as
it will go. Now squeeze the hose clamp and slide it up just a ways so
that it is about 1/2 inch down from the end of the hose.
Now press on the other end of the hose onto the turbo charger fitting.
Squeeze the hose clamp and slide it up to within about a half inch of
the top of the hose.
Now check and make sure that the hose is on good. Once you are sure then
proceed to reposition the air intake assembly placing it on the turbo
charger mouth and then sliding the hard plastic elbow back into the
air flow meter. Tighten the two large hose clamps and then position and
insert the air bypass hose, and the PCV hose in place and tighten their
respective hose clamps.
Check your work.
Now locate your test boost gauge (0-30 psi welding gauge), your 10-12
foot piece of 7/32 vacuum line, and your small plastic tee and short
two inch piece of 1/8 vacuum line.
Now we are ready to hook up our test boost gauge so that we can check the
actual boost the turbo is making. In the turbo charger section of your
shop manual on page EG-202 is a good diagram of where the welding gauge
needs to be inserted in line with the intake manifold and the absolute
pressure sensor. Look into the engine compartment on the passengers side
(US), and observe where the little dianostic port is, look just over and
then down from this. The dianostic port is at the rear of the engine
compartment up and across from the engine oil fill cap.
You will notice a small 1/8 inch rubber hose comming down and a small
white plastic knob inserted in it. Pull the 1/8 rubber hose off the
right side of the white plastic knob looking piece, then with a small
piece of 1/8 rubber hose on the plastic tee you purchased, connect one
side of the tee to the end of the white plastic knob looking piece.
Now press the end of the line that was on the white plastic knob
looking piece on to the other end of your tee. The 7/32 vacuum line
should be at the center of the tee, and then going over to your test
gauge. Position the hose and tee assembly so that it does not have any
kinks in it and then gently close, but don't completely close the
engine lid. The engine lid should be resting on the top part of the lock
such that there is more than sufficient gap that the 7/32 vacuum line
connected to the test gauge can come up out of the engine compartment and
not ge squeezed. I brought the hose then across the lower end of the
passenger side rear window, and secured it to the window glass with
a small piece of duct tape, then roll the passengers window partly down
and allow the hose and the gauge to go inside the car.
You are now ready to make your test boost readings. I would highly
recommend at this point, unless you can divide your attention, that you
have an assistant help you make the readings and help warn you if the
reading goes above 15 psi or so.
Take the car out and bring the car into full boost CAREFULLY AT FIRST,
and see what the boost reading is. If it is where you want it to be then
no further work need be done, just remove your test gauge and replace the
small 1/8 hose back to the proper place, and your done.
Otherwise you are going to have to backup in the proceedure and remove the
restrictor and drill out or make a new smaller one to bring the boost
into the range you desire.
WARNING AGAIN: be very careful not to exceed 17.5 psi boost on a stock
3S-GTE engine. When conducting your tests ease up on the
boost making sure that you do not exceed this maximum
limit.
Now enjoy the dramatic increase in power that your MR2 will have.
Contributed by Marc L. Summers
Back to Gunter Automotive Tech Page